by M.B., Survival Blog:
(Continued from Part 4.)
I couldn’t find the command to flip the parts in the menus of Prusa Slicer, but a right-click on the object allowed me to “Mirror” it. It took a moment’s thought, to make sure I mirrored the hinge box and brace in the right dimension (X, Y, or Z). Once I figured it out and mirrored the two parts, I was able to print a right-folding brace!
TRUTH LIVES on at https://sgtreport.tv/
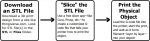
Have the Right Tools
A small collection of tools will help you process a new print into a finished item. Power tools are seldom needed.
-
Eye protection, and mask or respirator – Eye protection is an absolute must-have. If sanding or grinding polymer, a mask—or better yet, a respirator—will help to protect your lungs.
-
Nippers – a small pair of nippers for clipping supports from the project
-
Knife – a utility knife is okay, but I find a small, sharp, sturdy fixed blade knife, useful for both cutting and for light prying to pop supports loose. Mine is a kiridashi neck knife that I made from an old file.
-
Needle nose pliers – perfect for pulling pieces of filament out of small spaces.
-
Narrow wood chisel – an inexpensive chisel will be fine. Use it as a scraper that can reach into tight spaces and shave away filament, so that parts can fit into place.
-
Metric and SAE drill bits – for cleaning up/sizing holes in your project. The instructions enclosed with the files should tell you which sizes are needed.
-
Non-electric drill – an old school—very old school—hand drilling tool. An old-fashioned brace and bit is a great way to gently drill holes or clean up holes in polymer, while maintaining much greater control than with a handheld electric drill. In my opinion, a brace and bit is the only tool that comes close to substituting for a drill press for making holes in polymer. I started using mine for drilling the safety/selector holes in Polymer 80 AR receivers, and it’s ideal for that task. It can grip small bits, but larger bits I modify on a sanding disk in an electric drill. I grind four flats at the butt end of the large bit, creating a square, tapering shape. Look at some old-style bits for the brace, and you’ll see what I mean. You don’t need to remove a lot of metal from the rear of the bits. Available in antique stores, yard sales, and via eBay.
-
Pin vise – a heavy-duty pin vise is another tool that works very well for reaming out holes in polymer. It’s basically a chuck—for holding drill bits, awls or other small tools—at the end of a short handle. Mine handles up to a 1/4-inch bit. An okay substitute is a vise-grip, which is still better than trying to control a handheld electric drill in plastic.
-
Caliper – a dial or digital caliper is very useful for measuring or for verifying that something is the right size. Good ones are not inexpensive, but the dial caliper I bought over 30 years ago is still serving me very well.
-
A bench block (optional, but useful!) – this is an object for resting parts on when tapping pins in or out and for similar operations. You don’t need to buy one, as Thingiverse has free bench block files, for 3D printing. A bench block is very helpful for gun projects. It’s much better than resting an object on top of a roll of duct tape.
- 1/4-20 tap and tap handle (and drill bit) – the standard AR-15 grip screw has about one inch of 1/4-28 threads. When printing a receiver that takes an AR-15 grip, why bother with the unusual threading spec that is intended for 7075 aluminum? The very common 1/4-20 tap kit is easy to find and inexpensive, and I firmly believe the more coarse thread pattern is a better choice for polymer. I use common 1/4-20 x 1” socketed screws that take a hex key.
-
Soldering iron (optional, depending on your project) – used to install metal heat-set inserts used in some projects. Can also be used to stipple a grip, or to gently smooth out bad rough spots on polymer and/or to close small, cosmetic gaps between layers. Practice on some scraps of the same filament type and color, before risking a project that took 40 hours to print. Best used on dark colors.
-
Dremel tool (optional) – used with care and caution, a Dremel can be used to cut metal with a cut-off wheel. The sanding drums are also very useful. Grasp it firmly, but use it like a paintbrush or a pen, with a light, gentle touch.
-
Needle files, a small, fine file, and fine sandpaper – for cleaning up surfaces roughened by support material.
Don’t Forget Parts Kits, Rails, Etc.
Each firearm project usually comes with a shopping list in the instructions. Depending on the project, this may be a few, simple items from a hardware store (or already in your workshop). It may also be a collection of firearms parts, like the complete upper receiver of a MAC-11 9mm pistol. If the instructions ask for gun parts but don’t suggest a source, do some online searches. There is a whole industry of parts suppliers who support the 3D gun parts printing community.
Be Sure to Use Correct Pin Lengths
A number of 3D firearm projects use AR-15 trigger groups (hammer, trigger and disconnnector, along with two springs and two pins). Polymer receiver walls are usually thicker than those of aluminum AR-15 receivers, so mil-spec hammer/trigger pins may not be fully supported. Ideally, the ends of the pins should be flush with the sides of the receiver. Hammer and trigger pins are under stress. A short pin places that stress on a smaller amount of filament and may cause premature receiver failure. A full-length pin spreads the stress out over a larger area.